What Warehouse Automation Challenges Will I Encounter?
December 24th, 2024
4 min read
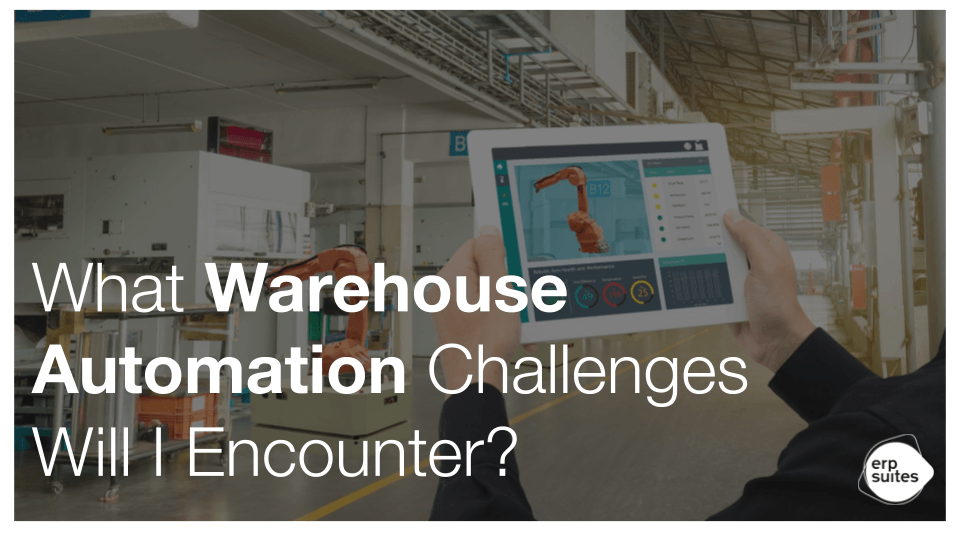
If you oversee a manufacturing floor, you know automating your warehouse processes is a gamechanger. More companies are putting automation into practice every day. With benefits like increased efficiency and smoother operations, who wouldn't?
But there are real costs and changes when it comes to putting automation into practice.
We get it. Anytime you undertake a technological change, it’s a good idea to have a trusted partner by your side. At ERP Suites, we have helped many of our customers completely transform the way they do business. We help them make their JDE work for them, and integrate new processes for long-term payoff.
Even with the best experts on your team, the road to automation can feel full of twists and turns.
Here are three challenges companies face when automating warehouse processes and how to overcome them.
What is Warehouse Automation
Warehouse automation refers to the use of technology to streamline operations. This includes conveyors, automated storage and retrieval systems (AS/RS), robotics, and barcode scanning,
Instead of relying solely on manual labor, automation helps:
- Move goods faster, reducing supply chain bottlenecks
- Reduce errors, boosting customer satisfaction
- Optimize space, maximizing your existing resources
Companies running ERP systems like JDE are increasingly integrating automation to stay competitive. Automation tools work seamlessly with JDE, providing real-time data on inventory and shipping. The Orchestrator, available starting with JD Edwards EnterpriseOne 9.2 and above, is one of JDE’s most powerful tools for initiating and executing automations for users.
Businesses can scale efficiently - without increasing cost - and meet customer expectations. But integrating new technology, managing data, and navigating changes isn't easy. That’s why understanding these hurdles helps to overcome them.
Challenge 1: How to Secure Buy-In and Prove ROI for Warehouse Automation
Warehouse automation systems can be costly, often ranging from hundreds of thousands to millions of dollars. Moving into automation and smart manufacturing can mean more efficiency, reduced labor costs, and fewer errors, but the business case isn’t always straightforward. To get the green light, you need two things: a clear ROI and buy-in from key stakeholders.
Let’s take Company A for example. They had done their homework, identified the bottlenecks, and calculated the potential savings. The ROI was clear; automation was the logical next step. But the project never moved forward. Why? They didn't have an internal stakeholder to rally the team and push the project to completion.
Without buy-in from leadership and someone to lead the charge, even the most promising automation projects can fizzle out.
How to Overcome It:
- Build a Compelling Business Case: Conduct a thorough analysis of your current operations. Identify pain points and find where automation will have the greatest impact.
- Engage Key Stakeholders Early: Identify champions within your organization who have a drive for process improvement. They can help advocate leadership, address concerns, and keep the project on track.
- Focus on Long-Term Value: Emphasize how automation helps scale operations without increasing costs. Highlight benefits like reduced labor costs, increased throughput, and fewer errors over time.
- Prepare for Change Management: Automation is a fundamental shift in how your warehouse operates. Make sure you have a plan to give staff clear communication, training, and ongoing support.
A clear ROI and strong internal buy-in makes the case for automation more compelling.
Challenge 2: System Integration Issues
Warehouse automation systems don’t operate in isolation. They need to integrate tightly with your core business systems, especially your JD Edwards. An AS/RS needs to sync with inventory data in real time for it to work properly. If this integration isn’t seamless, you’ll experience delays, errors, and operational bottlenecks.
Let’s say a warehouse employee is using an automated system to pick an item, but the inventory system doesn’t update immediately. The next order comes in, and the system still thinks the item is available. The employee fulfills the order, and then a domino effect starts. You end up short on inventory, orders are delayed, and customers are frustrated. Poor integration can disrupt the flow of your entire warehouse and beyond.
How to Overcome It:
- Understand System Capabilities: Understand the integration capabilities of both your existing ERP system and the new automated system to get the most out of them.
- Prioritize Real-Time Integration: Ensure data flows between systems in real time. Any delays or mismatches in data can create bottlenecks and errors.
- Test Extensively: Before going live, test your integrations to identify and resolve issues. Simulate real-world scenarios to ensure everything works in sync.
- Work with Integration Experts: Partner with experts or integration specialists to design reliable integrations.
Integrated systems make warehouse operations flow smoothly, keeping your inventory accurate. Take our customer in the waterworks manufacturing industry as an example.
Facing new compliance regulations in the United States, the company needed to ensure a certain type of product destined for international shipments never got mixed up with domestic shipments - tricky, because the products were virtually identical. ERP Suites built an automation using Orchestrations that tested for product accuracy, successfully solving the customer’s issue.
Challenge 3: Master Data and Integration Issues
Automation relies on accurate, up-to-date master data. This includes item dimensions, weights, storage locations, and product categories. If this data isn’t correct, your automated systems won’t function properly.
Say a warehouse manufactures a variety of items, from ornaments to bulky equipment. The AS/RS is tasked with retrieving a Christmas ornament to ship. The ornament is about 10 inches tall with a volume of 30 cubic centimeters. The system needs to know the exact size of the ornament and which box it will fit into.
But the master data is inconsistent, and the dimensions are incorrect. The AS/RS tries to place the ornament in a box that’s too small. The operation grinds to a halt. To make matters worse, the system needs to account for other items in the same box. Multiply this problem by hundreds of thousands of items. Add in complexities like hazardous materials, fragile goods, and government regulations. With the preponderance of human error and connection issues that can occur with legacy systems, data inaccuracies are not uncommon. Now you have a recipe for chaos.
How to Overcome It:
- Conduct a Data Audit: Review your master data thoroughly. Measure items, check storage locations, and verify product categories.
- Create a Data Governance Plan: Implement a Master Data Management (MDM) plan to ensure data is consistently maintained and updated. Assign responsibility for data quality to specific team members.
- Clean and Update Data Before Automation: Start cleaning and updating your data ASAP. This might involve physically measuring items or verifying data with suppliers.
- Continuous Data Maintenance: Regularly update and maintain your data to prevent future issues. Schedule periodic data reviews to keep everything accurate.
Clean, accurate data ensures your systems operate smoothly and helps prevent costly disruptions.
Bringing Automation to Your Warehouse is Easier Than You Think
From justifying the ROI to overcoming workforce resistance to managing data, the hurdles to automation are real. But with the right approach, transformation is possible.
Remember:
- Build a solid business case
- Ensure seamless system integration
- Maintain high-quality data
Learn how to integrate warehouse automation with your JD Edwards ERP.
Leyla Shokoohe is an award-winning journalist with over a decade of experience, specializing in workplace and journalistic storytelling and marketing. As content manager at ERP Suites, she writes articles that help customers understand every step of their individual ERP journey.